Project Story.03
ファインセラミックス部の
技術改善
ファインセラミックス製品の成形時の不具合、接合技術に関する不具合、ヒューマンエラーの発生を改善するため、FMEA手法を用いた分析と対策によって、製品歩留まりの向上を目指します。
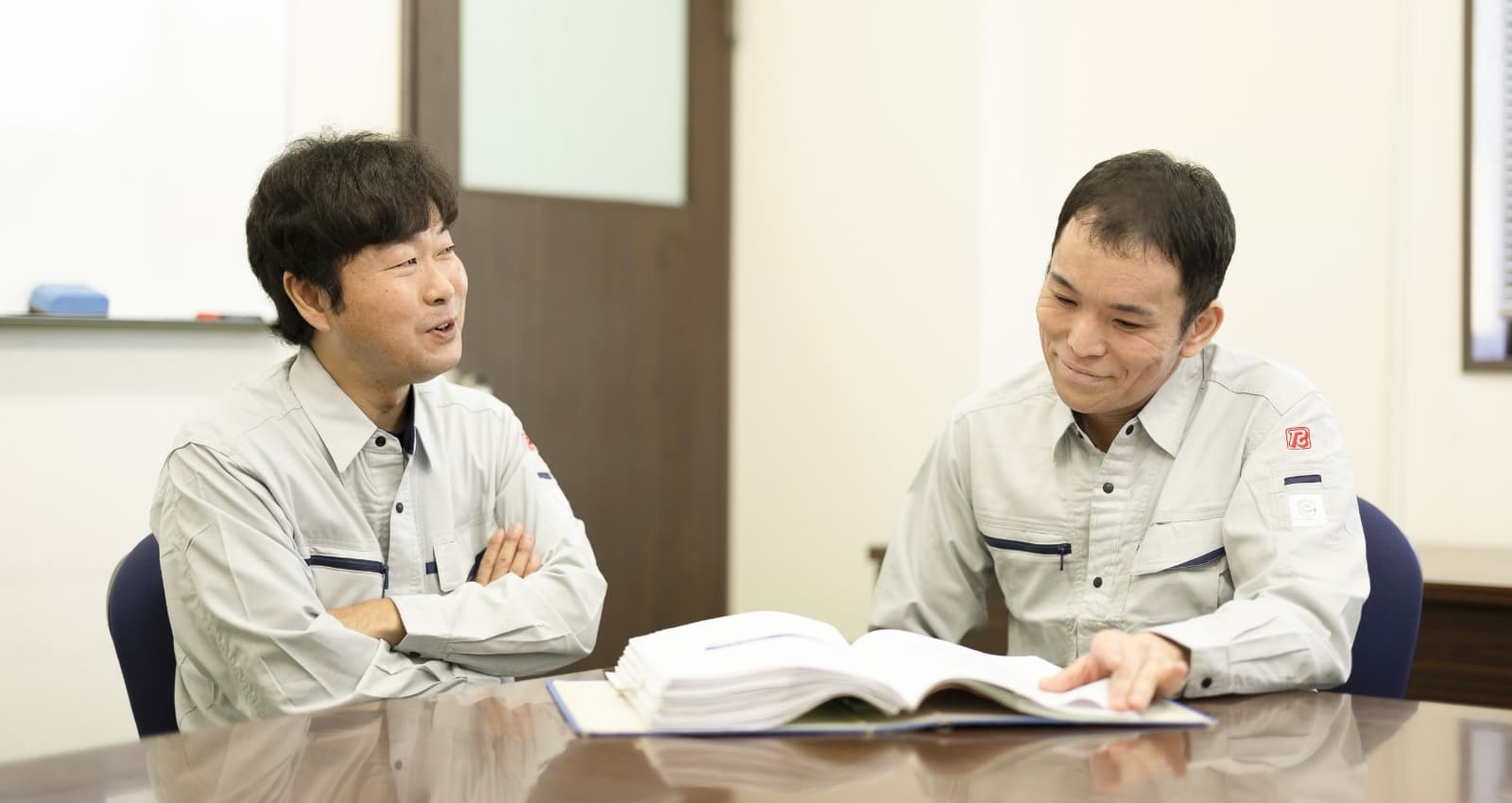
プロジェクトメンバー
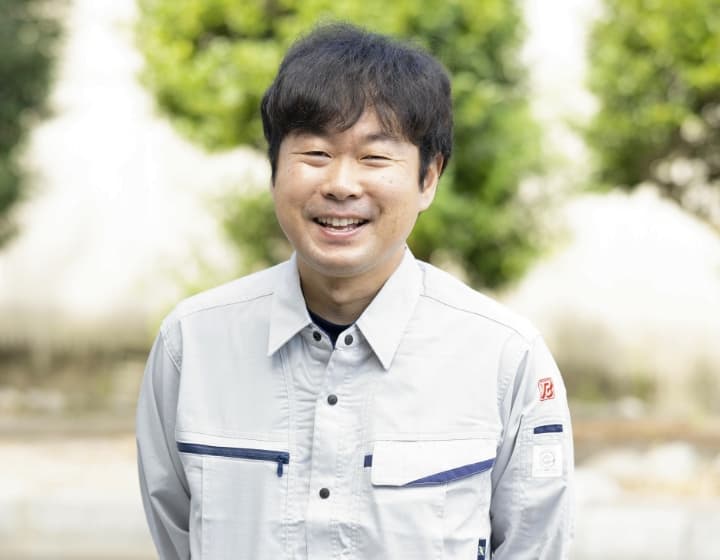
設計技術課長 T.H
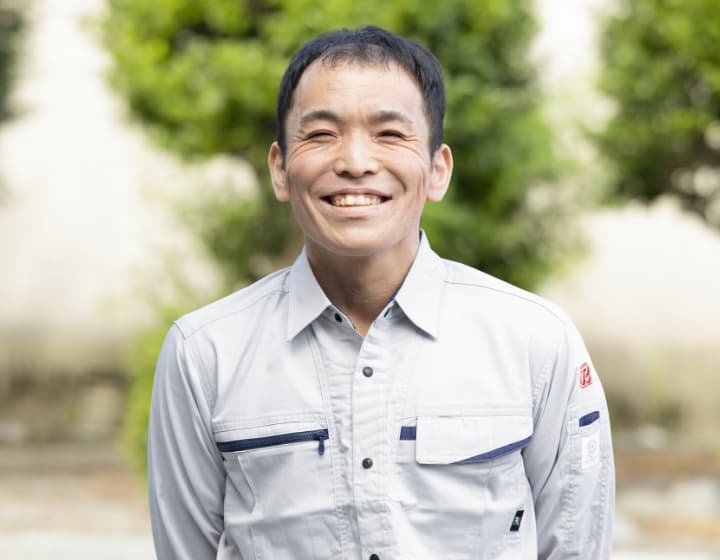
設計技術課主任 T.K
プロジェクトの背景と経緯
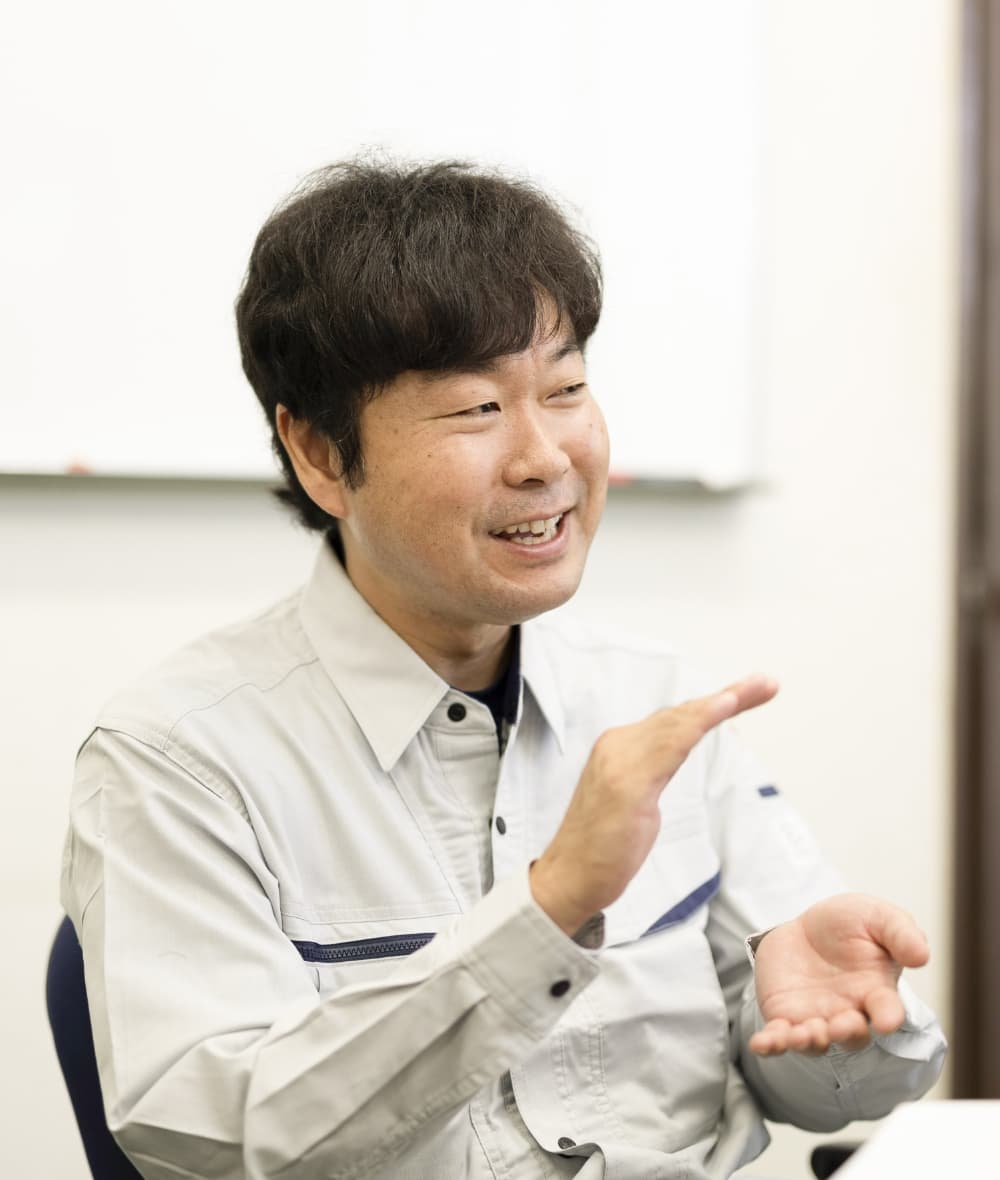
- T.H
- ファインセラミックス製品の製造において、製品に傷や割れが発生する不具合が毎年発生していました。それらを改善し製品の歩留まり(原料の投入量に対し、実際に得られた生産数量の割合)を向上させようということで、数値目標を設定して昨年から取り組んできましたが、一つを改善しても、別の箇所に不具合が出るという状況が続きました。とても難しいプロジェクトでしたよね。
- T.K
- はい。昨年の目標は「成形時の不具合改善」、「接合技術に関する不具合改善」、「ヒューマンエラーの改善」の3テーマでした。「接合技術に関する不具合改善」、「ヒューマンエラーの改善」の2テーマは目標を達成できました。
- T.H
- FMEA(故障モード影響解析のこと。故障・不具合の防止を目的とし、潜在的なリスクを洗い出す分析手法)を取り入れて、設計技術課だけでなく、各現場の社員を含めて約40人で取り組みました。不具合の原因と思われる要素を現場のみなさんから聞き出すことから始めました。
プロジェクトを進めるなかで、大変だったこと
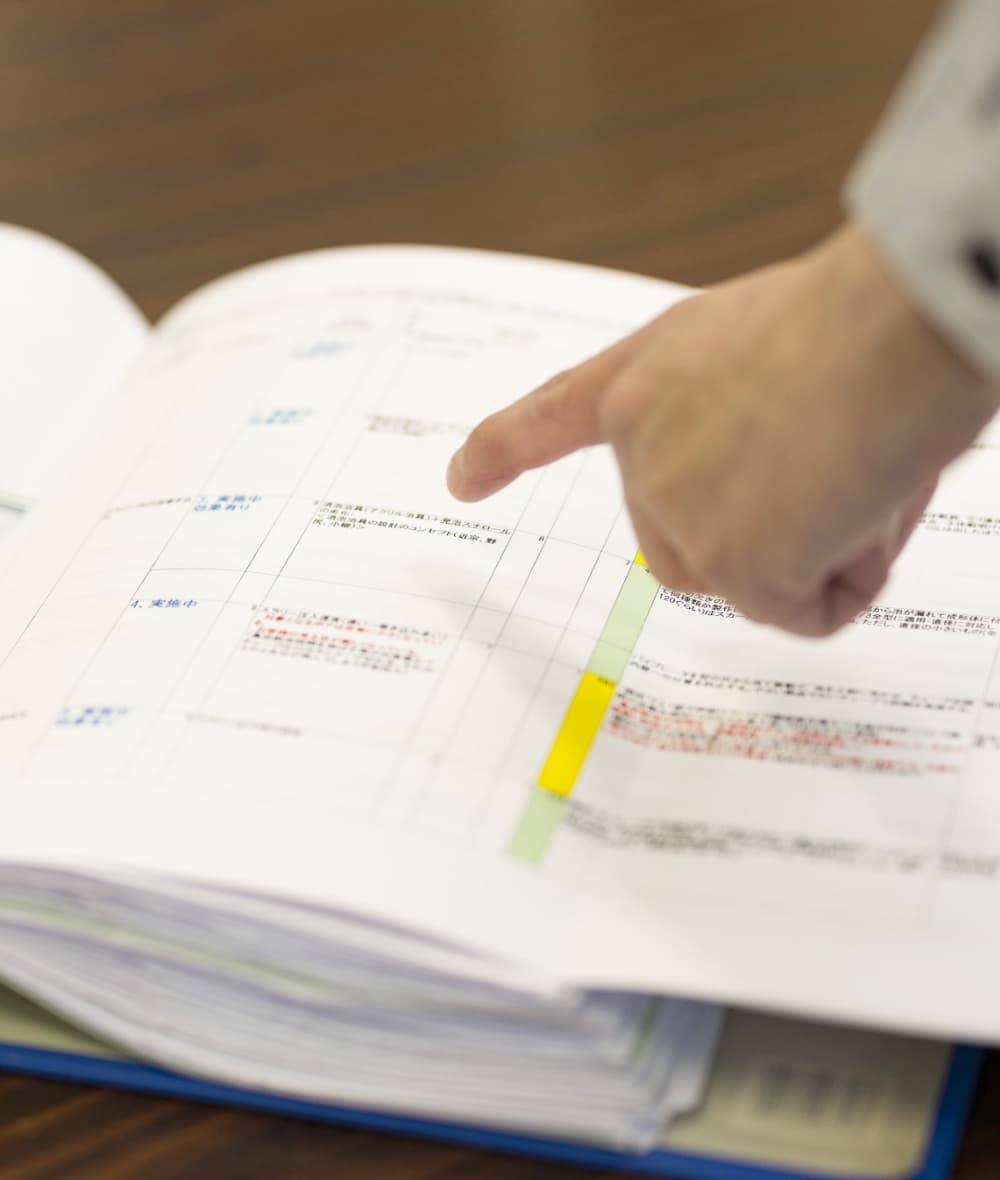
- T.H
- 不具合の原因を追及するために、工程担当者へヒアリングするのが大変でした。特にヒューマンエラーは、原因・要因解析が難しかったですね。ミスした当事者も原因を尋ねられると焦ってしまうし、なかなか最初から「○○が原因でミスをしました」と言えないのも、気持ちはよくわかります。
- T.K
- 「どうしてミスしたんですか?」と尋ねても返答が曖昧だったこともありました。FMEAで事前に洗い出していた要因以外に新たに出てくる要因もあって、思いも寄らない原因でミスは起こるものですよね。それは、当人にとっても言いにくいことだと思います。
- T.H
- 現場の方は責められているように感じてしまうのだろうな、と思いました。こちらとしては根本的な対策を講じるために追究しているのであって、決して責めているわけではないんですが…。
「成形時の不具合改善」のテーマでは、製品に大きな傷が入る原因がどうしてもわからなくて大変でしたよね。どこの工程で発生したかも特定できなくて。発生箇所を特定するために仮説を立てて、一定期間一つの工程を止めて経過観察をしてみても、不具合が発生して…。
- T.K
- そうやって仮説を一つ一つ検証しましたよね。製品をわざと壊して検証してみたこともありましたが、その時に原因を見つけ出したんですよね。衝撃の大きさのデータをとって、データの根拠も検証して。起きた事象を数値化することで説得力が生まれて、現場の方にも納得してもらうことができました。そこから練り上げた対策によって、不具合を改善することができたのですごくうれしかったです。
- T.H
- 解明には半年くらいかかりました。最初に仮説を立てて疑った工程の担当者には申し訳なかったけれど、快く検証につきあってくださったので本当に感謝しています。K主任もわたしも、セラミックスの材料力学や知識についてはまだまだ未熟な部分もあるけれど、だからこそ思い込みにとらわれず、色々な角度から原因を考えることができたのだと思います。
- T.K
- この案件から得た、思いがけない副産物もありました。職人技のような、熟練した作業者の感覚に頼っていた技術を数値化する方法を発見できました。ファインセラミックス製品は大部分を手作業によって作っているので、技術継承においても課題があったんですよね。結果的に一石二鳥になって、苦労した甲斐がありました。
プロジェクトにおける喜びと学び
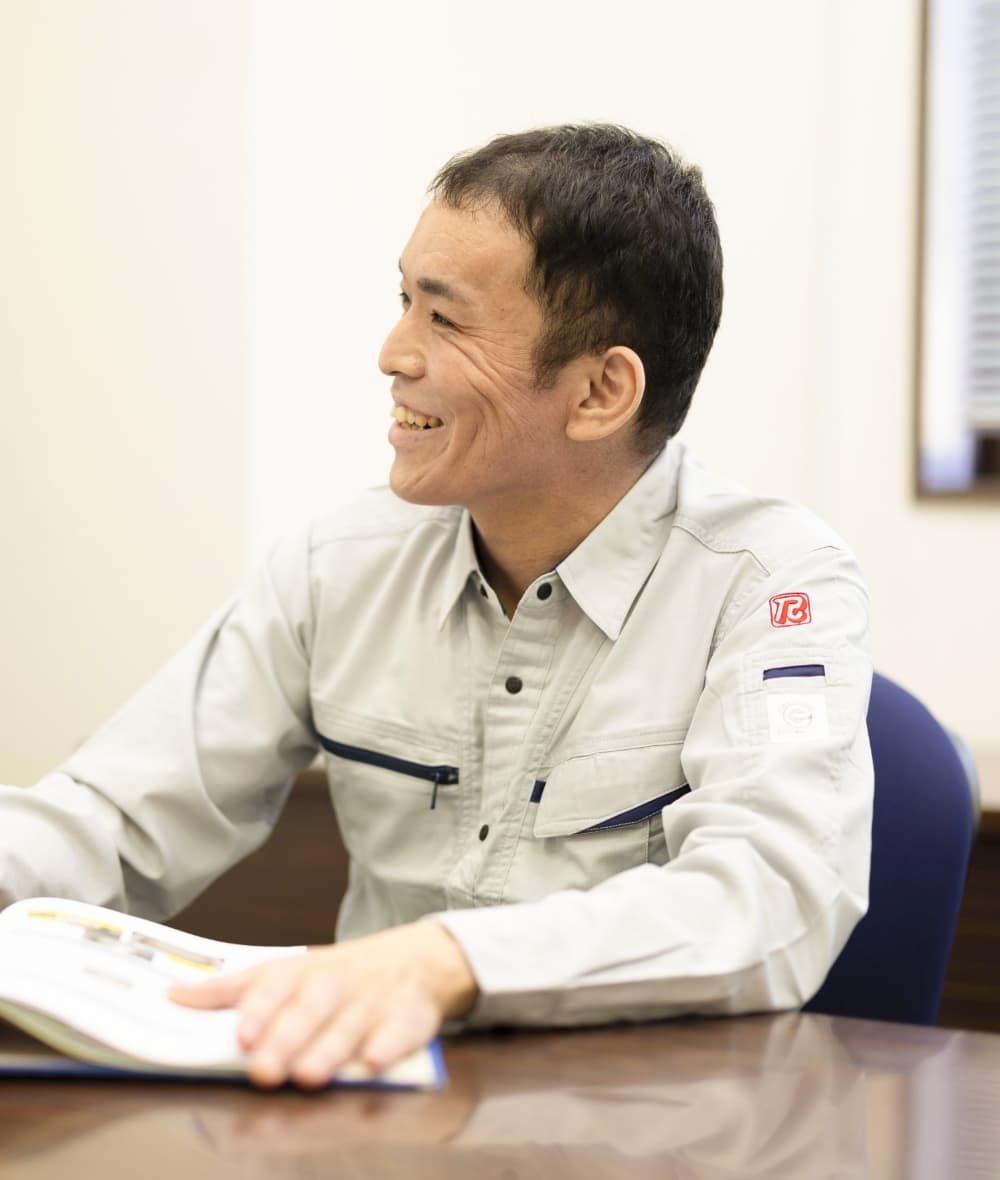
- T.H
- 歩留まりが向上したことによって納期遅延がなくなり、お客様や社内から評価されたことは素直にうれしかったです。そして何より、このプロジェクトは多くの社員のみなさんの協力があったからこそ成果を出すことができたのだと思います。学びとしては、周りの人の協力を得るためには、情報共有の方法と問題解決に対する熱意の伝え方が重要だと実感しました。不具合の発生は生産性の低下に繋がり、今よりもさらに忙しい状況を作ってしまうので、現場の方に改善したい理由をしっかり伝えました。その熱意を伝えるためにも、製造現場に何度も足を運んで直接コミュニケーションをとることが大事だと改めて実感しました。
- T.K
- 今回とった対策は、結果的に歩留まりが向上しているものの、従来よりも時間のかかる方法を採用しています。そういう意味では現場の方にご迷惑をかけてしまっているのですが、快く対応してくださって、とても助かっています。人の優しさ、温かさがうれしいです。
- T.H
- 今回の活動で、不具合の大部分がヒューマンエラー起因であることがわかりました。問題の根本をさらに辿ると、技術継承方法の問題や、作業ルールの不足など、さまざまな課題が浮かび上がってきましたね。それらの課題に対して、今年度からは設計技術課、生産課共同でヒューマンエラーを減らす取り組みをさらに推進させたいと思っています。
- T.K
- そうですね。今回用いたFMEA手法を他の製品にも展開して、リスクを減らす取り組みも続けていきたいです。それと同時に、設計の面でも、不具合のリスクを削減できる設計や、歩留まりが向上するような形状をお客様に提案することを心がけたいと思います。
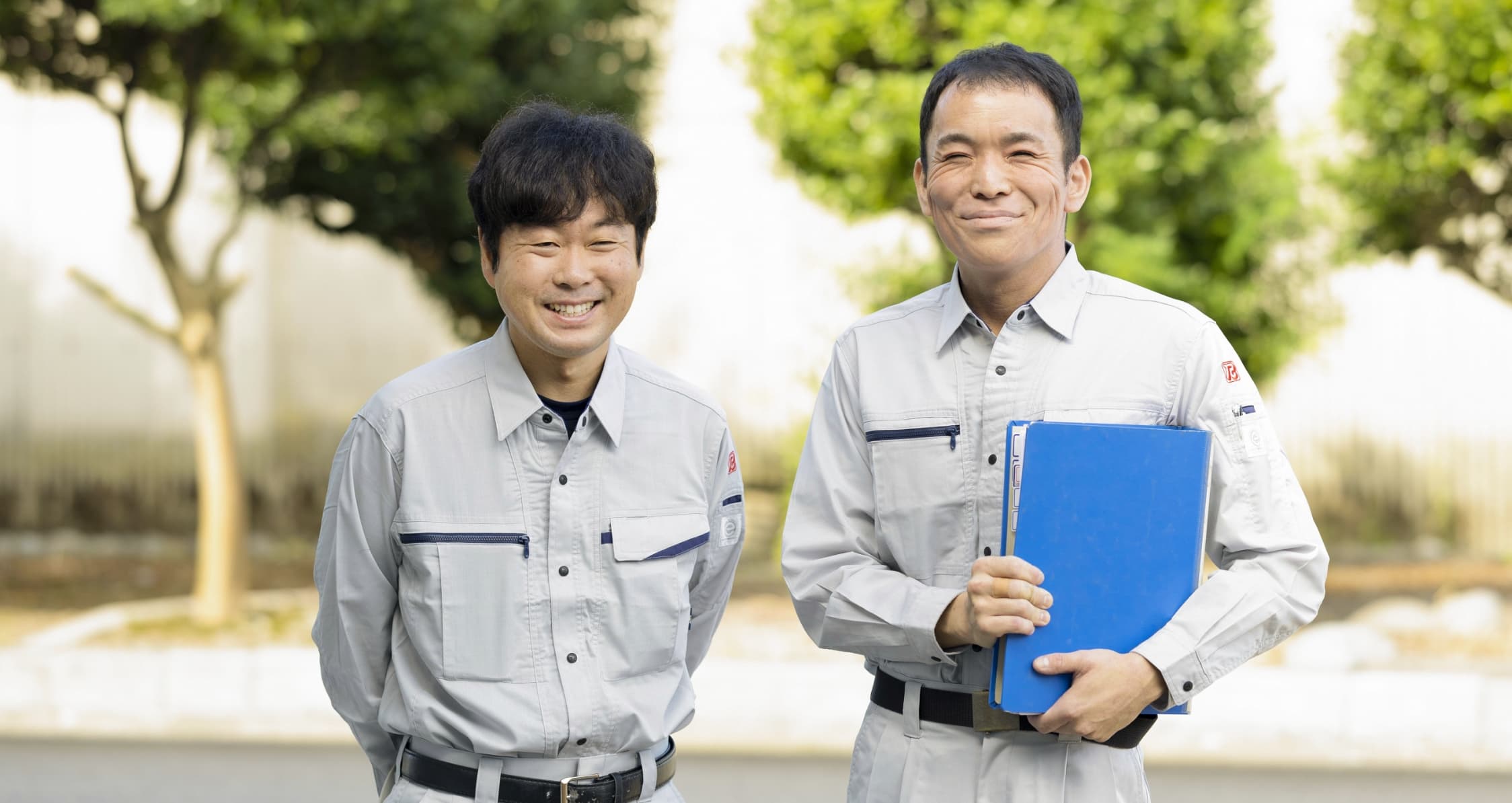